Logistics & Warehouse Storage Solutions
Optimizing Efficiency Across the Supply Chain
In today’s fast-paced, consumer-driven landscape, logistics operations face mounting pressure to meet rising eCommerce demands and the complexities of omnichannel distribution. From managing fluctuating inventories to ensuring accurate and timely deliveries, logistics providers must continually adapt to maintain efficiency and stay competitive. Operational efficiency requires dynamic solutions that optimize workflows, improve space utilization, and enhance throughput across the supply chain.
Whether it's navigating the challenges of third-party logistics (3PL), streamlining order fulfillment processes, or overcoming inefficiencies in truck loading and unloading, dynamic warehouse solutions are key to success. UNEX provides the solutions logistics operations need to stay agile, efficient, and prepared for whatever comes next.
Third-Party Logistics Warehouse Solutions
In the fast-paced world of logistics, third-party logistics providers face increasing pressure to accommodate fluctuating inventories, diverse SKUs, and rapid order fulfillment demands—all while keeping costs under control. Streamlined processes and efficient systems are essential for optimizing operations and maintaining agility, allowing 3PLs to meet their clients’ needs without costly expansions or inefficiencies.
UNEX Storage Solutions for 3PL Warehouses
UNEX provides solutions that help 3PL providers improve productivity, reduce labor costs, and enhance operational efficiency. From accelerating order picking and replenishment to ensuring seamless workflows and better space utilization, these dynamic solutions are designed to tackle the unique challenges 3PL warehouses face, including fluctuating demand, seasonal surges, and diverse inventory profiles.
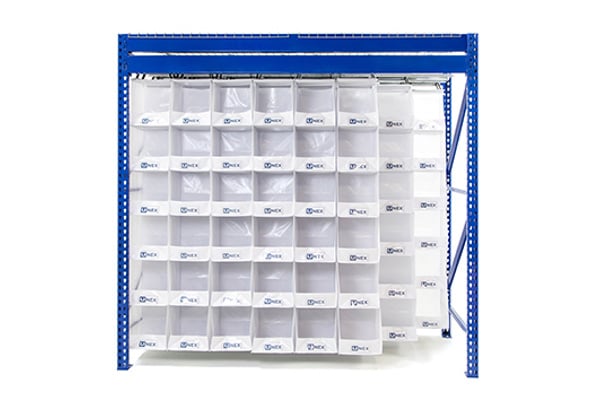
SpeedCell
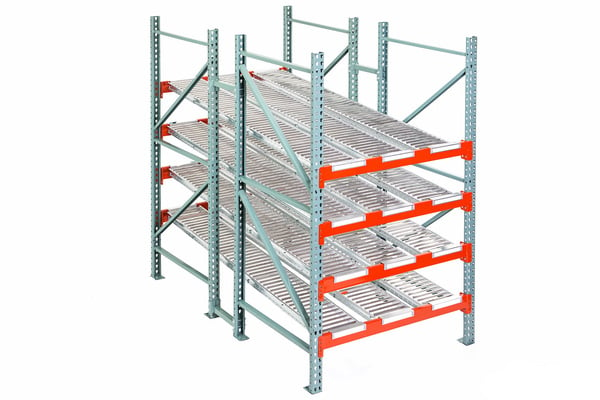
SpanTrack
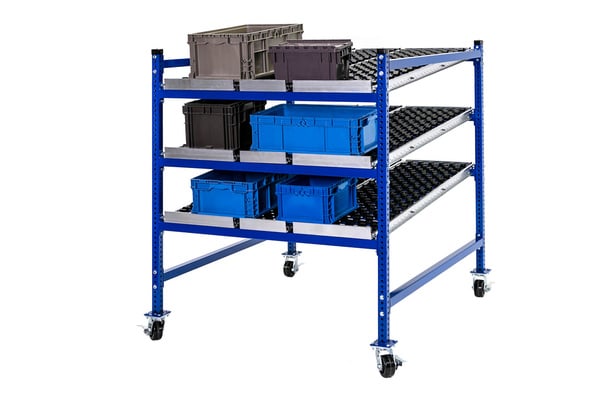
FlowCell
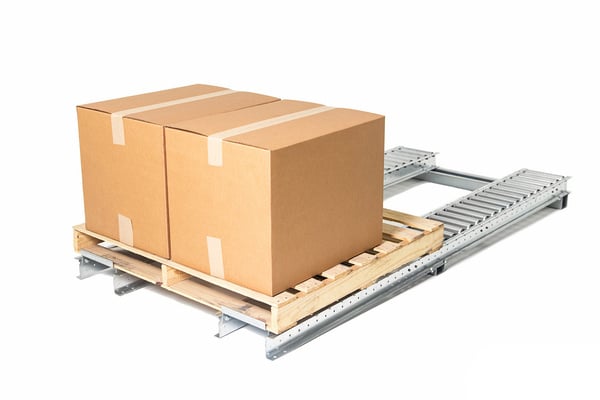
Pallet Track
Packing Station & Loading Dock Solutions
Efficient packing and loading operations are the cornerstone of smooth 3PL warehouse workflows, ensuring seamless transitions from order fulfillment to shipment. Challenges such as disorganized packing stations, labor-intensive processes, and dock inefficiencies can hinder productivity. UNEX offers a range of solutions to optimize packing stations and streamline loading docks, helping facilities meet rising demand with greater speed and accuracy.
UNEX Solutions for Packing & Loading
From modular packing stations to durable gravity conveyors, UNEX delivers 3PL fulfillment solutions that maximize efficiency and space utilization. These products enhance ergonomics, reduce bottlenecks, and create seamless workflows, allowing operations to pack and load orders faster while improving worker safety.
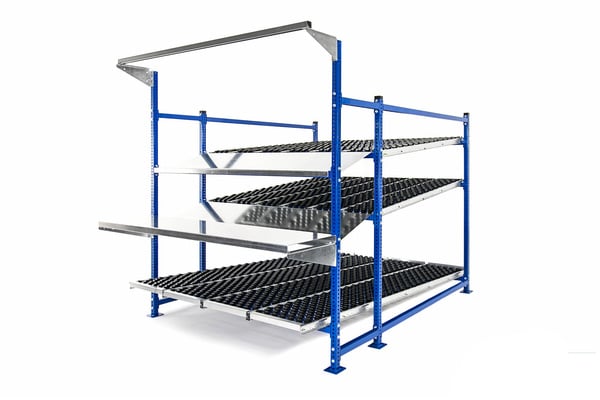
FlowCell
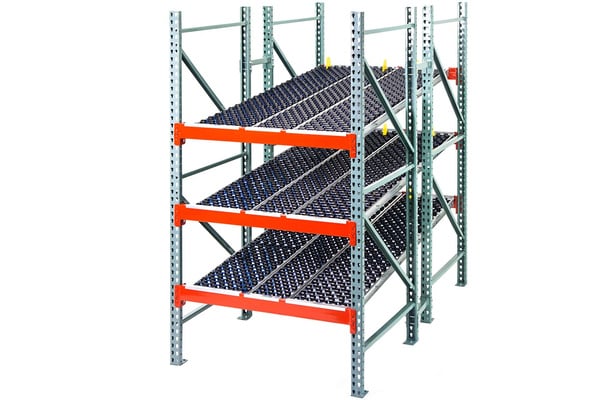
SpanTrack
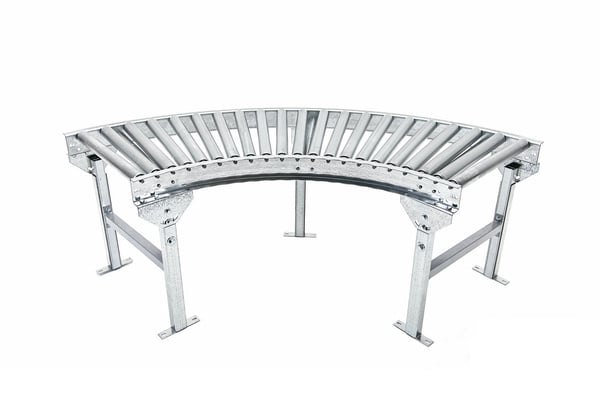
Gravity Conveyor
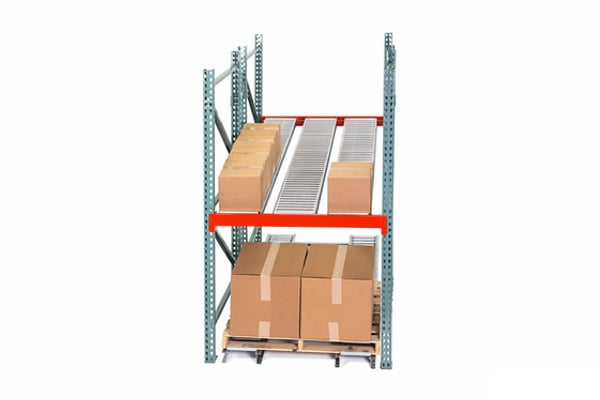
Pallet Track
Ready To Connect With An Expert?
Fill out the form below to request a consultation to find the ideal order picking solutions for your unique space.
Last Mile Delivery Solutions
The last mile is the most critical and challenging step in the supply chain, directly impacting customer satisfaction and loyalty. With rising delivery expectations and increased eCommerce demands, optimizing operations at fulfillment hubs closest to the end consumer is essential for success.
UNEX offers solutions to streamline last-mile workflows, ensuring cost-effective, on-time delivery while minimizing bottlenecks and operational inefficiencies.
UNEX Solutions for The Last Mile
UNEX offers a comprehensive range of solutions that enhance order picking, SKU management, and truck loading processes. These include dynamic storage systems for efficient inventory handling and versatile conveyor systems for seamless product movement. Designed to reduce labor costs, increase throughput, and improve operational agility, UNEX solutions empower facilities to meet the demands of last-mile logistics with precision and speed.
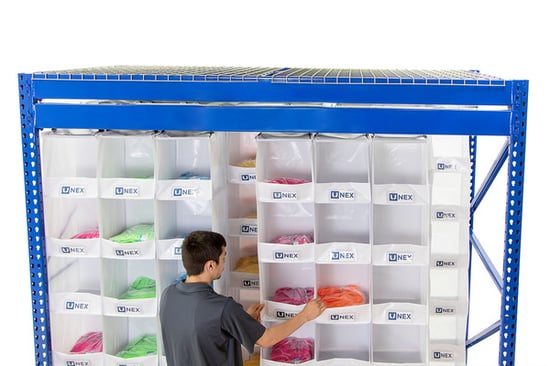
SpeedCell
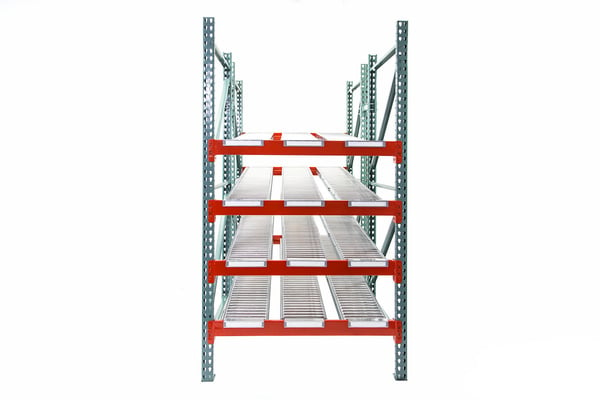
SpanTrack
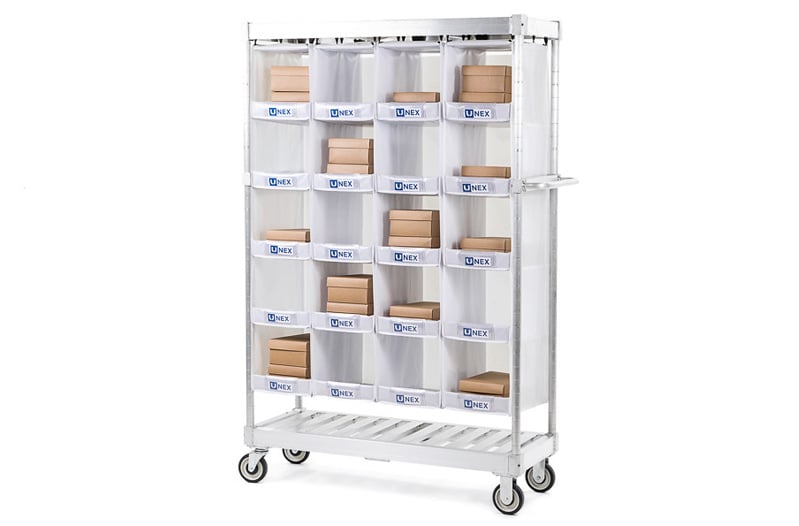
SpeedCartt
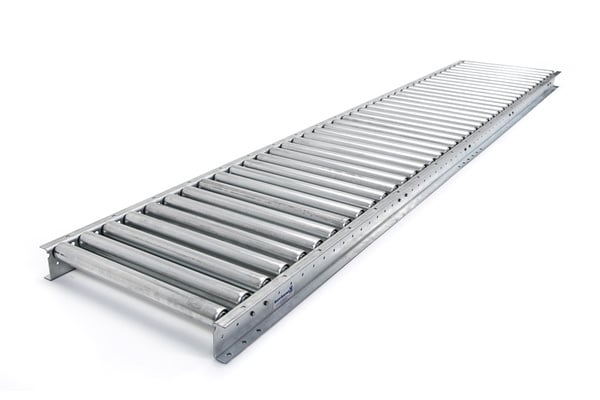
Gravity Conveyor
Warehouse Logistics Solutions
Efficient logistics within a warehouse or distribution center is essential for maintaining smooth operations across inbound, outbound, and internal processes. From receiving goods at dock doors to moving products through picking and packing areas and onto outbound trucks, optimized material flow reduces bottlenecks, enhances throughput, and lowers labor costs.
UNEX offers a range of solutions designed to address the challenges of warehouse logistics. These solutions focus on creating seamless pathways for product movement, improving worker ergonomics, and adapting to the ever-changing demands of distribution and warehouse environments.
UNEX Solutions for Warehouse Logistics
UNEX gravity conveyor systems simplify product handling across all stages of warehouse logistics. Whether permanent or portable, these systems enable flexible, efficient workflows tailored to the unique requirements of each operation.
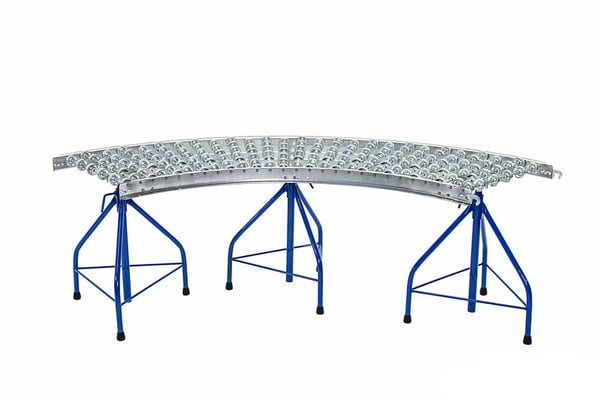
Portable Conveyors
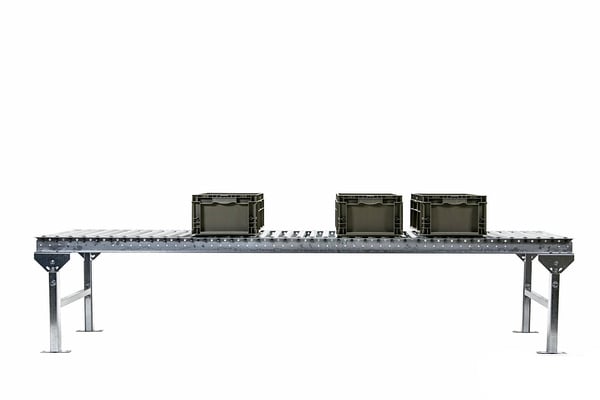
Permanent Conveyors
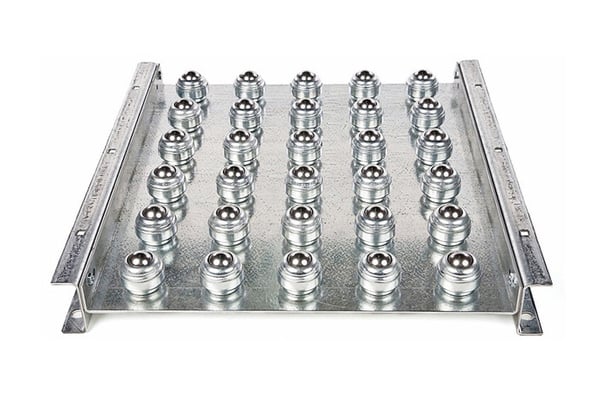
Ball Transfer Tables
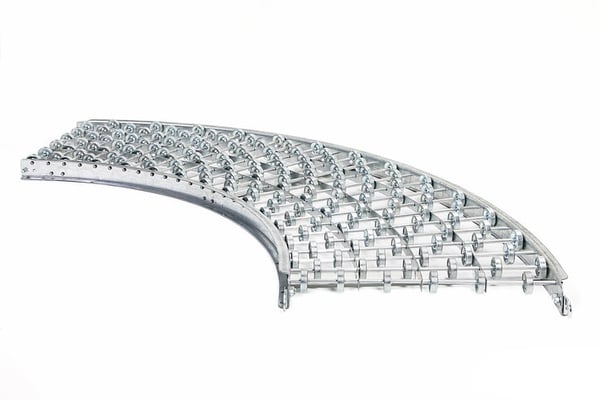
Curved Conveyors
Applications for Every Industry
Storage Solutions for 3PLs
Case Picking
Each Picking
Picking Carts
Resources
Explore All“The UNEX system makes inventory control easy. We can keep track of everything we have, so when our stores need a specific paint, we can find it fast and fulfill the order accurately.”
— Charles Aubuchon | VP of Distribution Center Operations | Aubuchon Hardware
“We are exceeding performance expectations, largely because of the efficient systems we have in place. The SpanTrack wheel beds are a big part of that picture.”
— Mark Alexander | Operations Manager | Cutter & Buck
“There’s no other storage solution like it. There’s nothing like SpeedCell. When a customer realizes SpeedCell will work for them, it’s the only solution.”
— Staci Deaton | Senior Partner | Indoff Inc.
Connect with an Expert
Get in touch with our team of experts to learn more about our solutions.